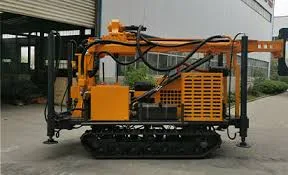
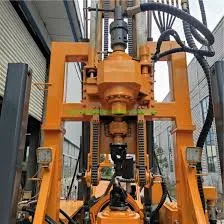
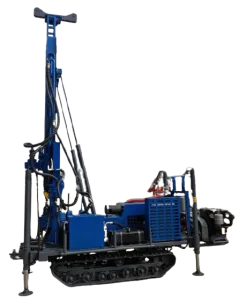
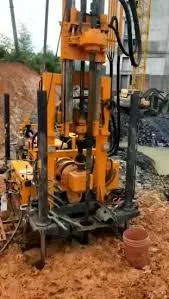
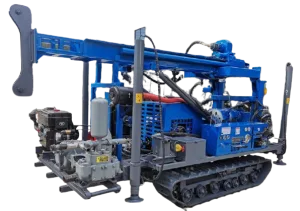
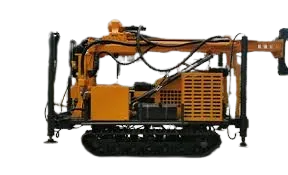
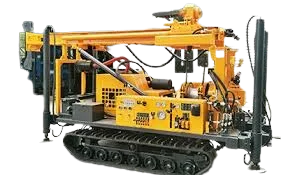
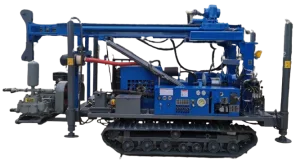
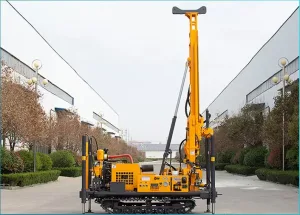
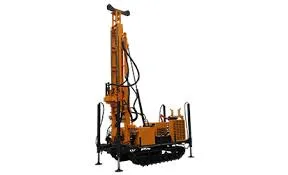
Análisis Técnico de la Perforadora M42-O
Especificaciones Técnicas de la M42-O
La M42-O es una plataforma de perforación multipropósito montada sobre orugas, diseñada para perforar pozos y sondeos hasta unos 300 metros de profundidad en terrenos mixtos (suelo y roca). Cuenta con un cabezal rotativo de transmisión mecánica (top drive mecánico) accionado por un motor diésel. En la Tabla 1 se resumen sus principales especificaciones técnicas:
Tabla 1: Especificaciones técnicas principales de la perforadora M42-O.
Parámetro | Especificación M42-O |
Profundidad máx. – Pozo (lodo) | ~200 m (pozo de agua, Ø152–203 mm) (hasta ~280 m en condiciones ideales). |
Profundidad máx. – Testigo NQ | 350 m (coring NQ) (hasta 600 m con diámetros menores). |
Profundidad máx. – DTH (aire) | 280–300 m (martillo neumático, Ø75 mm). |
Diámetro de perforación | 75 – 300 mm (rango típico, máx.≈300 mm). |
Torque máximo del cabezal | 9800 N·m (cabezal mecánico). |
Velocidad de rotación | 33 – 1120 rpm (10 marchas de avance; 2 en reversa). |
Fuerza de tiro (pull-up) | 10 Ton (≈100 kN) de capacidad de elevación. |
Fuerza de empuje (pull-down) | 5 Ton (≈50 kN) de empuje sobre la broca. |
Carrera del cabezal | 2.3 m (recorrido vertical del cabezal de potencia). |
Motor diésel | Yunnei YN27 – 42 kW (56 HP) @ 2400 rpm, 4 cilindros en línea. |
Chasis y traslación | Orugas de caucho (350 mm) o acero (300 mm); velocidad 0–2 km/h; pendiente máx. ~25°. |
Winche principal | 3–4.5 Ton (cabrestante mecánico de izaje, línea simple). |
Bomba de lodo | Opcional, modelos BW160/200/250 (triplex de pistones). |
Compresor (requerido) | Externo, 10.5–24.6 bar (1.05–2.46 MPa), 16–35 m³/min (según diámetro). |
Dimensiones | Transporte: ~4600 × 1900 × 2540 mm. En trabajo: ~3800 × 2200 × 5700 mm. |
Peso | ≈3.8 toneladas (configuración base, sin herramientas). |
Nota: Existen dos configuraciones: el modelo estándar M42-O (vertical) y una versión XM42-O actualizada (permite inclinación de mástil 75–90° y es más robusta, ~4.8 t de peso). La M42-O está diseñada para perforación multipropósito, combinando métodos de rotación con lodo y percusión con aire en un solo equipo.
Componentes Principales y su Análisis
A continuación, se analiza cada uno de los componentes y sistemas principales de la M42-O, describiendo su función y características técnicas relevantes:
Motor Diésel
La perforadora está impulsada por un motor diésel Yunnei de 4 cilindros modelo YN27 que entrega 42 kW de potencia a 2400 rpm. Este motor industrial, común en maquinaria pesada china, es enfriado por agua y opera con inyección mecánica directa de diésel. Provee la potencia necesaria para accionar tanto el cabezal rotativo como los sistemas hidráulicos auxiliares. Su cilindrada (~2.7 L) y diseño robusto le permiten ofrecer un desempeño confiable con un consumo de combustible moderado. El motor suele incorporar filtros de aire de dos etapas (para polvo) y sistemas de prefiltrado de combustible, adecuados para entornos polvorientos típicos de la perforación.
Análisis: El YN27 es un motor de baja a mediana potencia, suficiente para perforaciones hasta 300 m. Al ser un motor ampliamente utilizado, facilita la obtención de repuestos. Sin embargo, su potencia limitada implica que la eficiencia de transmisión es clave – justamente la M42-O aprovecha un cabezal mecánico de alta eficiencia para maximizar el uso de esos 42 kW. El motor requiere un mantenimiento rutinario (ver sección de Mantenimiento), pero tiene la ventaja de un diseño sencillo y probado.
Cabezal Rotativo (Top Drive Mecánico)
El cabezal de perforación de la M42-O es del tipo top drive mecánico, es decir, la rotación de la sarta de perforación se obtiene mediante transmisión mecánica (engranajes) desde la caja de cambios, en lugar de un motor hidráulico. Integra una caja de cambios manual de 5 velocidades (similar a la de un camión) que permite un amplio rango de velocidades de rotación del varillaje. El cabezal ofrece 10 marchas hacia adelante y 2 en reversa, logrando velocidades desde ~33 rpm hasta un máximo de 1120 rpm. Asimismo, cuenta con inversión de giro sensible y rápida (marcha atrás) para liberar herramientas atascadas o roscar/trocar tuberías. El par de salida máximo es de 9800 N·m, disponible en marchas bajas para atravesar formaciones duras.
El diseño mecánico incluye un conjunto de engranajes reductores de alta resistencia y un eje principal que transmite el torque directamente a la sarta. La transmisión mecánica tiene una eficiencia muy alta, minimizando pérdidas de potencia (por eso “duplica la eficiencia de transmisión” respecto a un sistema hidráulico equivalente). El cambio de marchas se realiza mediante embrague; el operador selecciona la velocidad según el método de perforación (baja velocidad/alto torque para DTH o tricono, alta velocidad para diamantino con broca de núcleo).
Análisis: El cabezal rotativo mecánico es el corazón del equipo. Su principal ventaja es la versatilidad de velocidad y torque: puede girar rápidamente para perforación con diamante o barrenas PDC en suelo blando, y también girar lentamente con enorme torque para barrenar roca dura o accionar un martillo de fondo. Esta amplia banda de operación en un mismo equipo es una característica distintiva de la M42-O. La contrapartida es que la operación requiere más pericia (el operador debe cambiar marchas manualmente) y el sistema mecánico añade peso al equipo. No obstante, el cabezal está diseñado para alta eficiencia energética, con mínimas pérdidas por fricción, lo que se traduce en menor consumo de combustible y menos generación de calor que en un cabezal hidráulico.
Sistema de Avance (Alimentación)
El sistema de avance controla el movimiento vertical (empuje y elevación) del cabezal a lo largo del mástil. La M42-O utiliza un mecanismo de doble velocidad de largo recorrido, accionado hidráulicamente, que proporciona una carrera útil de 2.3 m para el cabezal. Este mecanismo consiste en un cilindro hidráulico con poleas o un sistema telescópico que duplica la carrera efectiva, permitiendo un tramo largo de avance sin aumentar la altura del mástil. La fuerza de empuje (hacia abajo) es de 50 kN (5 toneladas) y la fuerza de tiro o izaje es de 100 kN (10 toneladas), suficiente para extraer la sarta de perforación con testigos y sacar tuberías entubadas de diámetro moderado.
El avance dispone de control hidráulico proporcional, lo que permite regular la presión sobre la broca según el método (por ejemplo, aplicar menos peso en perforación diamantina para no romper el testigo, o máximo empuje en DTH para mayor penetración en roca). La velocidad de avance también se puede modular, y el sistema de retorno rápido (descenso/ascenso acelerado) con doble bomba hidráulica reduce el tiempo no productivo al agregar o quitar barras.
Análisis: Un recorrido largo de alimentación reduce la frecuencia de adicionar barras (cada barra es de 1.5 o 2 m), mejorando la productividad y disminuyendo riesgo de atoros o sobrecalentamiento de broca. La capacidad de 10 toneladas de tiro es notable para un equipo compacto – asegura poder retirar herramientas atascadas y manejar tubos de revestimiento en pozos de agua. El mecanismo hidráulico de avance complementa al cabezal mecánico, aportando control fino de la tasa de penetración y amortiguando impactos. En resumen, el sistema de avance de la M42-O combina fuerza y precisión, siendo fundamental para adaptarse a distintos métodos de perforación.
Chasis, Orugas y Estabilización
La M42-O está montada sobre un chasis de orugas tipo excavadora, disponible en orugas de caucho (para proteger pavimentos y reducir vibraciones) o acero (mayor durabilidad en terreno rocoso). El ancho de oruga estándar es ~350 mm, proporcionando estabilidad en suelos blandos. El tren de orugas le permite desplazarse con facilidad en terrenos irregulares a una velocidad de hasta 2 km/h. Puede superar pendientes de alrededor de 25° en configuración de oruga de caucho (o ~20° con orugas de acero más pesadas).
El chasis incorpora patas de nivelación hidráulicas (gatos estabilizadores) en las esquinas, que se despliegan durante la perforación para nivelar la plataforma y transferir la carga al suelo. Estas patas aseguran una base firme, reduciendo vibraciones y oscilaciones del mástil. El mástil de la M42-O en el modelo estándar es vertical fijo (90°), pensado para perforación recta hacia abajo; en la versión XJDL puede inclinarse hasta 75° para perforaciones angulares.
Análisis: El sistema de orugas le brinda a la M42-O movilidad autónoma en campo, pudiendo llegar a sitios remotos o de difícil acceso (laderas, terrenos sin caminos). Su huella relativamente compacta (~1.9 m de ancho) permite incluso ingresar por senderos estrechos. La opción de orugas de caucho es útil en entornos rurales o urbanos donde se requiera no dañar el suelo. La estabilidad durante la perforación está bien lograda mediante los gatos hidráulicos; no obstante, debido a su peso moderado (~3.8 t), en formaciones muy duras puede requerir reducir avance para evitar vibraciones excesivas. En general, el chasis cumple con brindar portabilidad y estabilidad, dos cualidades cruciales para equipos multipropósito en terrenos mixtos.
Bomba de Lodo
Para la perforación rotativa con lodo (circulación directa de fluido), la M42-O típicamente se equipa con una bomba de lodo de pistón triplex, usualmente modelo BW160, BW200 o BW250 según las necesidades. Estas bombas de lodo son accionadas por el motor diésel (directamente o a través de la transmisión auxiliar) o mediante un motor separado, y sirven para inyectar fluido de perforación (mezcla de agua/bentonita) por el interior de la tubería de perforación. Por ejemplo, el modelo BW160 puede entregar caudales de hasta ~160 L/min a 2.5 MPa de presión, adecuado para sondeos profundos con barrenas de diámetro pequeño. Modelos mayores (BW250) logran caudales y presiones más altos, útiles para perforar pozos de mayor diámetro.
Análisis: La bomba de lodo es esencial para la perforación rotary convencional – el fluido lubrica la broca, enfría la herramienta y acarrea los recortes hacia la superficie. La M42-O no lleva integrada una bomba de lodo fija (es un accesorio opcional); esto brinda flexibilidad para seleccionar la bomba adecuada a cada trabajo o incluso operar sin lodo (usando solo aire) en ciertos casos. El operador puede montar la bomba sobre la misma unidad o en un remolque aparte. En cuanto al desempeño, la capacidad de mover hasta ~200 L/min de lodo permite perforar orificios de diámetro medio (ej. 6” u 8”) manteniendo una buena limpieza del pozo. Es importante asegurar una correcta mantención de esta bomba (reemplazo periódico de empaquetaduras, válvulas y aceite) para evitar fallas que detengan la perforación.
Compresor de Aire
Para las modalidades de perforación neumática (martillo de fondo DTH o rotación con aire), la M42-O requiere el apoyo de un compresor de aire externo de alta capacidad. Las especificaciones recomiendan un compresor capaz de suministrar entre 16 y 35 m³/min de aire, a una presión entre 10 y 24 bar. En la práctica, esto significa utilizar un compresor tipo tornillo de ~250-350 PSI (17–24 bar) con caudal de 600–1200 CFM, similar a los usados en perforación de pozos profundos. Por ejemplo, para lograr 300 m de profundidad con martillo DTH de 34”, podría emplearse un compresor de ~25 bar y 20 m³/min. El compresor se conecta a la perforadora mediante mangueras, alimentando al cabezal y bajando por dentro de las varillas hasta el martillo de fondo.
Análisis: La capacidad de usar aire comprimido convierte a la M42-O en una perforadora dual (aire/lodo). En terrenos donde el uso de lodos es difícil (p.ej. zonas carst o formaciones que absorben el fluido), la opción neumática es invaluable. Sin embargo, el compresor no está incorporado en la máquina, lo que implica logística adicional (transporte del compresor) y un costo operativo considerable (el consumo de diésel de un compresor potente es alto). Aun así, esta separación es ventajosa: se puede elegir el compresor según la necesidad del proyecto o incluso alquilarlo independientemente. La M42-O está diseñada para soportar la perforación con aire a alta presión – tiene conexiones y mangueras preparadas para ello, y un cabezal robusto capaz de resistir las vibraciones del DTH. Un buen manejo del compresor (presiones adecuadas, uso de lubricador de línea para el martillo) permitirá un rendimiento óptimo en el modo neumático.
Winche (Cabrestante)
El equipo viene provisto de un winche mecánico principal montado en el mástil, con una capacidad de izaje de entre 3 y 4.5 toneladas (dependiendo de la configuración). Este cabrestante es accionado mecánicamente (por toma de fuerza de la transmisión) y utiliza cable de acero para izar herramientas, tuberías o revestimientos durante la perforación. Se emplea típicamente para levantar o bajar la sarta de perforación en operaciones de sondeo con recuperación de testigo (coring), para extraer tubos de revestimiento (casing) en pozos, o para ayudar en maniobras de instalación de bombas, etc. La velocidad de arrollamiento es variable según la marcha seleccionada y la capa de cable en el tambor. Además del winche principal, la M42-O puede equipar un winche auxiliar hidráulico de ~1.5 T (opcional) para manejo de herramientas o sondeos de menor escala.
Análisis: El winche mecánico de 4.5 T complementa la capacidad del sistema de avance. En perforación con diamantina (testigo), por ejemplo, se emplea el winche para maniobrar la columna de sondeo y los barriles recuperadores de núcleos. Su accionamiento mecánico directo ofrece potencia constante y confiable; sin embargo, requiere que el motor diésel esté funcionando y aplicar frenos manualmente. La capacidad de ~3–4 toneladas en línea simple puede aumentarse usando aparejos (poleas) si se necesita más fuerza de izaje, aunque a costa de velocidad. En comparación con equipos hidráulicos, este winche mecánico tiene menos fineza de control pero mayor simplicidad (menos propenso a fugas o fallas súbitas si se mantiene bien). Es importante que el operador verifique el estado del cable de acero, frenos y seguros antes de cada operación de elevación por seguridad (ver sección de Seguridad).
Sistema Hidráulico Auxiliar
Aunque el cabezal de rotación es mecánico, la M42-O posee un sistema hidráulico robusto para accionar otras funciones: avance del cabezal (cilindro principal), gatos de nivelación, dirección y traslación de orugas, y opcionalmente el winche auxiliar y/o un dispositivo de sujeción de tuberías. El sistema hidráulico utiliza doble bomba de aceite para optimizar el desempeño: durante la perforación activa, funciona solo una bomba (priorizando control fino), y al levantar/descender rápidamente la sarta se acoplan las dos bombas en flujo combinado para mayor velocidad y potencia. Esta tecnología de división y convergencia de caudal permite reducir las pérdidas de potencia y minimizar tiempos muertos al agregar tubos o tramos de varilla.
La presión de trabajo del sistema hidráulico suele estar en el orden de 16–20 MPa para accionar los cilindros. Incluye tanques de aceite hidráulico con filtros, válvulas de control y distribuidores que el operador manipula mediante palancas. Por ejemplo, hay válvulas para subir/bajar el mástil (avance), para accionar cada gato de forma independiente, y para mover las orugas adelante/atrás y girar (steering) la máquina.
Análisis: El sistema hidráulico es el encargado de aportar flexibilidad y control a la máquina. Gracias a él, funciones como la nivelación y alimentación son precisas. La implementación de doble bomba es un diseño inteligente que ahorra energía: evita recirculación innecesaria de caudal cuando no se requiere, y aporta potencia extra solo cuando es necesario (al retirar tubería rápidamente, por ejemplo). Esto reduce la carga parasitaria sobre el motor y disminuye el calentamiento del aceite. Como todo sistema hidráulico, requiere mantenimiento preventivo (filtros limpios, mangueras en buen estado) para asegurar su fiabilidad. Una ventaja de la M42-O es que, al tener menos sistemas hidráulicos (no usa motor hidráulico para la rotación), la probabilidad de sobrecalentamiento del aceite es menor y la gestión de la potencia es más simple. En resumen, el sistema hidráulico auxiliar de este equipo está bien dimensionado para soportar las operaciones críticas sin añadir complejidad innecesaria al cabezal de perforación.
Tuberías de Perforación
La M42-O puede trabajar con diferentes tuberías de perforación según el método y el diámetro requerido. Para perforación de testigo (diamantina), es compatible con varillaje de estándar exploratorio: por ejemplo, barras NQ, HQ, PQ (que corresponden a diámetros exteriores ~76, 89 y 114 mm respectivamente). De hecho, el fabricante indica específicamente tuberías NQ/HQ/PQ como coincidentes con el cabezal. Para perforación de pozos de agua, típicamente se usan tuberías más robustas de Ø76 mm (3”) o Ø89 mm (3½”) de diámetro exterior, generalmente en longitudes de 1.5 m o 2.0 m por tramo. Estas tuberías de acero vienen con roscas macho-hembra endurecidas (normalmente rosca tipo API REG o similar en pozos, y rosca estándar W en diamantina).
El equipo también puede manejar tubería de revestimiento (casing) para entubar pozos de agua durante la perforación en terrenos colapsables. Gracias a la alta fuerza de tiro (10T), es posible instalar y extraer tramos de tubería de revestimiento de diámetro moderado (por ejemplo 6” o 8”) siguiendo el avance de la perforación en gravas sueltas, utilizando un sistema seguidor de tubería si está disponible (casing advancer).
Análisis: La versatilidad en tuberías es un punto fuerte de la M42-O. Puede emplear tubos delgados para exploración geológica profunda con extracción de testigo (donde la prioridad es alcanzar gran profundidad con diámetro mínimo), y también usar tubería de mayor diámetro para perforar pozos de agua convencionales. El equipo no dispone de una mesa rotaria convencional, por lo que el cambio de varillaje se hace suspendiendo la sarta con el cabezal y usando llaves de boca o llaves de cadena para desenroscar. En este sentido, muchos equipos similares incorporan un quebravarrillas hidráulico o mordazas para sujetar la tubería durante el apriete/afloje – en la M42-O podría ser un accesorio opcional montado en la base del mástil. Las barrenas (tuberías con aletas helicoidales) también pueden usarse en la capa superficial para iniciar el pozo, aunque el método principal es circulación de fluido. En cualquier caso, es crucial elegir tuberías de buena calidad y compatibles con la capacidad de torque del equipo, para evitar fallos de rosca o doblado de barras bajo altas cargas.
Accesorios y Herramientas
La M42-O admite una amplia gama de herramientas de perforación y accesorios, lo que la convierte en un equipo verdaderamente multipropósito. Entre los accesorios típicos se incluyen:
- Brocas tricónicas y PDC: Para perforación rotativa con lodo en roca o formaciones compactas. La máquina puede operar brocas tricónicas de diámetros desde ~115 mm hasta 300 mm. Las brocas de diamantes polycristalinos (PDC) sin núcleo también se pueden usar en suelos duros pero relativamente homogéneos.
- Martillo de fondo (DTH) y barrenas de aire: La M42-O trabaja con martillos neumáticos externos (generalmente de 3” a 6” de diámetro) acoplados a la última varilla. Esto permite perforar a percusión en roca dura con aire. Se usan bit de martillo (botones de carburo) del diámetro requerido (75–203 mm típicamente).
- Corona y barril de diamante: Para sacar testigos, se usan coronas impregnadas o de diamante natural en tamaños AQ, BQ, NQ, HQ, PQ, junto con barriles recuperadores de núcleo adecuados a cada diámetro. La alta velocidad del cabezal permite una perforación diamantina eficiente.
- Sistema de inyección de agua/espuma: Al perforar con aire en ciertos suelos, se puede inyectar agua o espuma para controlar el polvo y estabilizar cortes. Se suele equipar un inyector de espuma (bomba pequeña) y un compresor auxiliar para tal fin, aunque no es parte intrínseca del equipo.
- Herramientas geotécnicas (SPT): Dada su versatilidad, el equipo puede realizar ensayos SPT (Standard Penetration Test) en perforaciones geotécnicas. Para esto se utiliza un martillo de caída libre acoplado al cabezal o al winche para hincar el sampler estándar en el fondo del pozo. La propia empresa vendedora destaca que permite realizar SPT además de otras tareas de exploración.
- Otros: Trépano de barrena helicoidal (auger) para suelos blandos superficiales, tubos de revestimiento con zapatas cortadoras para perforación con entubación simultánea (utilizando el torque del cabezal para hincar el casing), subs y adaptadores para conectar diferentes tipos de rosca, etc.
Análisis: Los accesorios correctos amplían las capacidades operativas de la M42-O. En un día, el equipo podría iniciar perforando con barrena helicoidal en los primeros metros, luego cambiar a rotación con lodo y tricono en arcillas, y finalmente instalar un martillo DTH para atravesar un estrato de roca dura – todo con el mismo equipo base. Esta flexibilidad es una de las razones por las que se promociona como “multipropósito”. No obstante, cambiar de método implica tiempo (por ejemplo, retirar el tricono y montar el martillo DTH) y contar con el equipamiento complementario (como compresor de aire, bombas, etc.). En resumen, la M42-O puede adaptarse a numerosas situaciones de perforación gracias a su compatibilidad con diferentes herramientas, lo que la hace muy valiosa en proyectos variados (ver Aplicaciones típicas).
Ventajas Técnicas del Cabezal Mecánico (vs. Cabezal Hidráulico)
El diseño de la M42-O con cabezal rotativo de transmisión mecánica conlleva varias ventajas técnicas frente a equipos equivalentes con cabezal hidráulico. Entre las principales se destacan:
- Mayor eficiencia de transmisión: Al tener conexión mecánica directa (engranajes) entre el motor y la rotación, se minimizan las pérdidas de potencia. La transmisión mecánica aprovecha mejor la potencia disponible, duplicando la eficiencia en comparación con un sistema hidráulico equivalente y reduciendo el consumo de energía ~35%. En otras palabras, menos potencia se disipa en forma de calor hidráulico, traduciéndose en mayor torque útil en la broca con el mismo motor.
- Amplio rango de velocidades y torque: El cabezal mecánico con caja de cambios ofrece una gama muy amplia de RPM, desde muy bajas hasta altas (33–1120 rpm) con ajustes en 5 marchas. Esto permite adaptar óptimamente la velocidad al terreno: alta velocidad para perforar con brocas de diamante en roca (donde se requiere 700–1000 rpm) y baja velocidad pero máximo torque para operar un martillo DTH o broca tricónica en roca dura. Un cabezal hidráulico típicamente tiene un rango más limitado (p. ej. 0–150 rpm), optimizado solo a ciertos métodos.
- Versatilidad de métodos en un solo equipo: Gracias al punto anterior, la M42-O puede integrar funciones de perforación con lodo y con aire en una sola plataforma, con un solo cabezal. No necesita equipos separados para diamantina vs. DTH; el mismo cabezal mecánico puede con ambos. Esta integración funcional resuelve las dificultades de perforar con martillo en terrenos blandos y la baja eficiencia de perforar con lodo en rocas duras.
- Menor mantenimiento complejo: Un cabezal mecánico evita el uso de motores hidráulicos de alta potencia, bombas de gran caudal y complejos sistemas de control electrónico asociados. Esto suele implicar menores costos de mantenimiento y reparación, al prescindir de componentes hidráulicos caros (motores, mangueras de alta presión) que requieren técnicos especializados. De hecho, el equipo se describe como de “fácil mantenimiento y bajo costo” de operación.
- Robustez y fiabilidad: Los sistemas mecánicos bien diseñados (engranajes, ejes) tienden a ser muy duraderos y resistentes a picos de carga. Un cabezal mecánico tolera mejor la vibración intensa de un martillo de fondo y los golpes, en comparación a un motor hidráulico que podría dañarse por cavitación o sobrepresión. Además, la M42-O tiene menos sensores y componentes electrónicos, lo que reduce las posibilidades de fallas inesperadas en campo.
En resumen, la elección de un cabezal mecánico en la M42-O proporciona eficiencia energética, versatilidad y simplicidad. Estas ventajas la hacen más eficiente y ahorrativa que equipos hidráulicos comparables, especialmente en proyectos de larga duración o en zonas remotas donde la facilidad de mantenimiento es clave.
(Nota: En la siguiente sección se discutirán también las contrapartidas o desventajas de este diseño, para equilibrar la comparación.)
Desventajas y Limitaciones del Modelo M42-O
Si bien la M42-O ofrece importantes ventajas, es importante reconocer algunas limitaciones o desventajas inherentes a su diseño y categoría, en comparación con otros equipos:
- Operación más manual y dependiente del operador: El uso de una transmisión mecánica implica que el operador debe cambiar marchas manualmente para ajustar la velocidad de rotación. Esto requiere cierta experiencia y entrenamiento para hacerlo en el momento adecuado (normalmente se debe detener la rotación para cambiar de marcha, usando embrague). En cambio, los equipos con cabezal hidráulico suelen tener control continuo de velocidad mediante válvulas o accionamiento eléctrico, lo que simplifica la operación. La M42-O, por tanto, demanda un operador atento y conocedor de la máquina para aprovechar al máximo su rendimiento.
- Menor control de precisión en la rotación: Aunque cubre un amplio rango de RPM, la velocidad en la M42-O se ajusta en escalones fijos (marchas) más la modulación del acelerador del motor, pero no es infinitamente variable. Un sistema hidráulico permite un control stepless muy fino de la velocidad y torque aplicado, que puede facilitar ciertas operaciones delicadas (por ejemplo, romper un testigo sin sobre-torque). En la M42-O el control es adecuado pero menos suave, lo que puede resultar en variaciones de par más bruscas al cambiar de marcha o régimen.
- Pausas por cambios de marcha: Ligado a lo anterior, cada vez que se necesita cambiar la velocidad de rotación de forma significativa (por ejemplo, pasar de alta velocidad en suelo blando a baja velocidad en roca dura), el operador debe interrumpir la perforación momentáneamente para cambiar la relación de la caja de cambios. Esta detención puede reducir ligeramente la productividad en comparación con un cabezal hidráulico que ajusta la velocidad sin detenerse. En la práctica, el impacto es menor si el operador planifica los cambios con anticipación y aprovecha para hacer otras tareas durante esas pausas.
- Ángulo de perforación limitado (en modelo estándar): La versión base M42-O solo perfora vertical (90°). No es posible inclinar el mástil para perforaciones anguladas a menos que se tenga la versión actualizada XJDL que permite de 75° a 90°. Muchos equipos hidráulicos montados sobre camión u orugas permiten inclinaciones para estudios geotécnicos inclinados o instalación de micropilotes en ángulo. En la M42-O estándar, esto sería una limitación si el trabajo requiriera ángulos diferentes a vertical.
- Peso y robustez moderada: Con ~3.8 toneladas, la M42-O es relativamente liviana comparada con taladros hidráulicos de capacidad similar (que suelen pesar 5–7 t). Si bien esto es una ventaja en transporte, también significa que tiene menos masa para amortiguar vibraciones y estabilizar la perforación en formaciones muy duras. En roca competente a gran profundidad, un equipo más pesado puede mantener mejor la presión sobre la broca sin “rebotar”. La M42-O puede requerir reducir el avance o usar barras pesadas adicionales para compensar esto en ciertos casos.
- Componentes mecánicos sujetos a desgaste: La caja de cambios, embrague y engranajes del cabezal requieren mantenimiento periódico y ajustes (ej. tensado de embrague, cambios de aceite en la transmisión). Si el mantenimiento se descuida, pueden presentarse averías costosas (un engranaje dañado, por ejemplo). Por otro lado, en un sistema hidráulico, aunque también hay desgaste, este se distribuye entre bombas y motores que pueden ser más fáciles de intercambiar modularmente. En cambio, reparar una transmisión mecánica puede implicar intervenciones más laboriosas.
- Nivel de ruido y vibración: Los equipos hidráulicos modernos suelen ser más silenciosos y con menos vibraciones percepibles, gracias a la amortiguación del fluido y aislamientos. Un sistema mecánico transmite directamente las vibraciones del proceso de perforación a la estructura. Por tanto, la M42-O puede generar más ruido mecánico (engranajes, motor a alta revolución) y vibraciones que un equipo hidráulico equivalente. Esto podría ser un factor a considerar en entornos urbanos o sensibles al ruido, donde tal vez se requieran medidas de mitigación (cabinas acústicas, etc.).
En resumen, las principales desventajas del modelo M42-O derivan de su propia simplicidad mecánica: menos automatización y menor fineza de control comparado con un equipo hidráulico de alta gama, y ciertas limitaciones físicas (ángulo fijo, peso). Sin embargo, muchas de estas contrapartidas son manejables con buen entrenamiento del personal y mantenimiento adecuado. Para muchos usuarios, las ventajas en costo y versatilidad superan estas desventajas, pero es importante tenerlas en cuenta al planificar un proyecto con esta perforadora.
Capacidades de Perforación de la M42-O
Una de las fortalezas de la M42-O es su carácter multipropósito, pudiendo aplicar diferentes métodos de perforación según el tipo de terreno y los objetivos del proyecto. A continuación, se describen las capacidades de perforación por método, indicando profundidades aproximadas alcanzables y usos típicos de cada uno:
- Perforación rotativa con lodo (rotary/mud drilling): La M42-O puede perforar en circulación directa de lodo, utilizando brocas tricónicas o barrenas PDC sin extracción de testigo. En suelos arcillosos, arenas compactas y rocas fracturadas, este método es eficiente para avanzar rápido. Con varillaje delgado (Ø42–60 mm) se han logrado profundidades de hasta 500+ m en condiciones ideales, mientras que para pozos de agua de diámetro amplio (152–203 mm) se recomienda alrededor de 150–250 m de profundidad para mantener un buen caudal de lodo y limpieza del pozo. La rotación con lodo es ideal para atravesar formaciones blandas a medianamente duras, obteniendo recortes en superficie para análisis geológico. La M42-O ofrece alta velocidad (hasta 1120 rpm) que ayuda a una acción de corte eficiente de las barrenas en roca blanda a media dureza.
- Perforación con martillo de fondo (DTH) con aire: En presencia de roca dura y maciza, la opción de martillo neumático es fundamental. Acoplada a un compresor adecuado, la M42-O puede accionar un martillo de percusión de fondo de diámetro entre ~3” y 6”. Este método logra una rápida penetración en rocas ígneas o metamórficas duras, donde la rotación convencional sería muy lenta. La profundidad efectiva con DTH depende del diámetro y compresor; con un martillo de 3” (75 mm) se pueden alcanzar hasta 280–300 m en roca firme, mientras que con martillos más grandes (6”, ~152 mm) la profundidad económica suele ser menor (100–200 m) debido a mayores requerimientos de aire. La M42-O ha sido diseñada para este modo: su cabezal mecánico provee el torque necesario para girar el martillo y sus engranajes resisten bien la vibración de la percusión. Se destaca la capacidad de alternar: “aire y lodo en un solo equipo” para resolver tanto la perforación de roca dura como la de suelos sueltos en el mismo pozo.
- Perforación con broca tricónica (rotación en roca con lodo): Entre el rango de muy duro (DTH) y blando (barrena/espiral), está la perforación con tricona y lodo en roca consolidada de dureza media-alta. La M42-O, con su alto torque (9800 N·m), puede hacer girar brocas tricónicas grandes de hasta ~12” (305 mm) en formaciones sedimentarias o calizas fracturadas. Este método es útil en pozos de agua profundos donde se atraviesan capas rocosas competentes pero se prefiere usar circulación de lodo (por ejemplo, para traer detritos a superficie cuando el martillo no sería eficaz por agua en el pozo). Se han manejado diámetros de 115–220 mm con tricona satisfactoriamente. La velocidad de rotación típica en tricona es baja (50–80 rpm) y la M42-O puede sostenerla indefinidamente en sus marchas bajas. La capacidad de bombeo de lodo (con bomba BW250) permite mantener despejada la zona de corte de la tricona. Este método, aunque más lento que DTH en roca dura, tiene la ventaja de obtener detritus para análisis y de no requerir compresor de aire de alta presión.
- Perforación diamantina (extracción de testigo): La M42-O puede equiparse con un barril de recuperación de testigo (coring) para exploración geológica. Empleando tubería delgada (NQ, HQ) y coronas impregnadas de diamante, es capaz de obtener testigos (núcleos) de roca de alta calidad hasta profundidades significativas. Según especificaciones, puede lograr ~350 m con NQ (testigo de 47.6 mm) e incluso más (500–600 m) con diámetros de testigo menores, aunque a esas profundidades la velocidad de perforación disminuye. La ventaja del cabezal mecánico aquí es su alta velocidad (hasta 1120 rpm) que es similar a la de equipos de sondeo dedicados. Los usuarios han reportado que con la M42-O se pueden realizar campañas de exploración minera/geotécnica obteniendo núcleos continuos de roca con calidad satisfactoria, lo cual evidencia la dualidad de la máquina: un taladro de sondeo geológico combinado con perforadora de pozo. Durante el coring, se utiliza el winche para sacar los barriles y la bomba de lodo para circulación inversa (en sondeo wireline).
- Ensayos SPT y perforación geotécnica: Como se mencionó, la máquina permite realizar Standard Penetration Tests (SPT) y otros ensayos in-situ. En terrenos aluviales o arcillosos, se puede perforar con tricono hasta la profundidad deseada y luego hincar el sampler estándar con el martillo de 63.5 kg cayendo desde 760 mm, utilizando el cabezal o el winche para levantar el martillo. De esta forma, la M42-O puede logar integrarse en estudios geotécnicos para fundaciones, facilitando tanto la perforación como la obtención de N-value en el mismo pozo. Asimismo, se pueden extraer muestras inalteradas de suelo blando mediante tomamuestras Shelby, usando la presión hidráulica del avance para hincarlos. Esta capacidad multiuso (SPT, núcleos, etc.) es resaltada por distribuidores como parte de su versatilidad “todo en uno” en investigaciones de terreno.
- Otros métodos complementarios: La M42-O puede emplearse para reperforar pozos existentes, hacer reamed (escariar) agujeros a mayor diámetro en fases sucesivas, o incluso perforar con espuma/aire en formaciones cavernosas (inyectando espuma para cargar los ripios). Su estructura y potencia también le permiten, con modificaciones menores, realizar micropilotaje o perforación de anclajes en suelo, aunque para estos casos la falta de inclinación en el modelo base es una limitante. Finalmente, dada su fuerza de empuje de 5T, es posible hincar tuberías o samplers como un equipo de penetración superficial.
En síntesis, la M42-O puede abordar múltiples técnicas de perforación sin salir del sitio, cambiando simplemente de herramienta y ajuste operativo. Esto la hace muy adecuada para terrenos “mixtos” donde se alternan capas blandas y duras: el operador puede comenzar con lodo y barrena, luego pasar a aire y martillo en roca, retornando a lodo si aparece otra sección más blanda, todo con la misma máquina. Pocas perforadoras en su rango de precio ofrecen esta flexibilidad. No obstante, aprovechar todas estas capacidades requiere contar con el equipamiento auxiliar (brocas, compresor, bomba) y con personal capacitado para cambiar de método eficientemente sobre la marcha.
Opiniones Reales de Usuarios en Condiciones Similares
Para valorar el desempeño de la M42-O en la práctica, es útil conocer la experiencia de usuarios reales que han operado este equipo en perforaciones ~300 m en terrenos mixtos. En general, las opiniones coinciden con las capacidades proclamadas por el fabricante, destacando la versatilidad y eficiencia de la máquina, aunque también señalan algunas consideraciones prácticas:
- Versatilidad comprobada en campo: Usuarios en América Latina y África reportan que la M42-O realmente puede enfrentar una variedad de suelos. Por ejemplo, en Chile se comercializa como “KIT 280 Multipropósito”, enfatizando que puede perforar con diamantina, con martillo de fondo o tricona, e incluso hacer ensayos SPT con el mismo equipo. Esta versatilidad ha permitido a pequeñas empresas de perforación acometer proyectos diversos (pozos de agua, exploraciones mineras, estudios geotécnicos) sin tener que subcontratar diferentes equipos, lo cual supone un ahorro significativo y mayor autonomía. En terrenos donde se alternan capas duras y blandas, los operadores valoran poder cambiar de método rápidamente, comentando que “la máquina se adapta bien al terreno” al poder usar lodo o aire según convenga.
- Profundidad y rendimiento realistas: Si bien en teoría el equipo puede llegar a 280–300 m en pozo de agua, varios usuarios mencionan que habitualmente perforan hasta ~200 m de profundidad de forma eficiente, especialmente en pozos de 6 a 8 pulgadas. A profundidades mayores, la velocidad de perforación disminuye y es necesario ser paciente, pero la máquina lo consigue. En exploración diamantina, lograr 300+ m de testigo NQ es factible, aunque los perforistas recomiendan usar barras HQ o NQ solamente (evitando PQ a máxima profundidad) para no sobrecargar el equipo. En suma, las cifras de capacidad presentadas son alcanzables pero en la práctica los operadores suelen trabajar dentro de rangos conservadores para maximizar la productividad y la vida útil del equipo.
- Ahorro de costos y combustible: Un aspecto reiterado por dueños de equipos es el bajo costo operativo de la M42-O en comparación con perforadoras hidráulicas. Gracias a su motor de 42 kW y transmisión eficiente, el consumo de diésel es moderado. Un contratista comentó que puede perforar un pozo de 150 m con menos combustible que equipos mayores harían 100 m. Además, el costo inicial de la máquina es menor (se cita un precio en torno a USD $25,000 por unidad base, frente a $50,000 o más de equipos hidráulicos similares), lo que la hace accesible a emprendimientos pequeños. Esto se alinea con la estrategia de venderla como una opción de “precio realmente conveniente” para perforistas locales.
- Facilidad de transporte y montaje: Usuarios en zonas rurales aprecian que la unidad cabe en un camión pequeño o remolque y que no requiere grúa para su descarga, pues puede descender por sus propios medios (orugas). El peso liviano facilita cruzar puentes precarios o terrenos blandos. Un perforista en África mencionó que pudo remolcar la M42-O hasta áreas remotas donde equipos más grandes no llegarían, destacando su portabilidad. El montaje en obra es rápido: en pocas horas se puede nivelar e iniciar perforación, dado que la máquina es autónoma (trae sus gatos hidráulicos y mástil integrado).
- Curva de aprendizaje y operación: Por otro lado, las demandas sobre el operador son un tema citado. Algunos relatan que al comienzo hubo una curva de aprendizaje para dominar el cambio de marchas y el “feeling” de la perforación mecánica. Operadores acostumbrados a equipos hidráulicos debieron adaptarse a controlar embrague, acelerador y palancas manuales. Sin embargo, una vez dominado, el consenso es que la máquina es fiable y sencilla. La ausencia de complejos sistemas electrónicos hace que muchos problemas se solucionen con mecánica básica. Un usuario experimentado señaló que es importante “sentir el equipo” – es decir, escuchar el motor y notar la resistencia en la broca para saber cuándo cambiar a marcha baja o cuándo aliviar peso, algo que viene con la experiencia.
- Mantenimiento en campo: Las experiencias indican que la M42-O requiere disciplina en mantenimiento, pero no es excesivamente exigente. Varios usuarios recomiendan cambiar el aceite de la transmisión con mayor frecuencia de la sugerida, especialmente tras largas jornadas en altas temperaturas, para garantizar la longevidad de los engranajes. También mencionan llevar siempre repuestos de filtros de aire y combustible, y grasa para los puntos de engrase, ya que las condiciones polvorientas aceleran la necesidad de servicio. En general, reportan que con un buen mantenimiento preventivo (ver sección siguiente) el equipo tiene pocas averías mayores. No obstante, hubo casos en que un mal uso del embrague derivó en su desgaste prematuro – algo evitable con capacitación y cuidado.
- Limitaciones observadas: Como era de esperar, se confirman algunas limitaciones: en roca extremadamente dura (granito masivo grado F<20), la perforación con tricona resultó lenta y finalmente se optó por usar DTH en la mayor parte del tramo duro. Esto evidencia que para ciertos contextos (p. ej. todo el pozo en basalto compacto) quizás un equipo 100% DTH más pesado tendría ventaja. Sin embargo, en contextos de terreno mixto, los usuarios concuerdan en que la M42-O “hace el trabajo” cumpliendo con las expectativas. Otro punto mencionado es la vibración: al operar DTH, la máquina vibra considerablemente, por lo que es vital anclar bien los gatos y vigilar las conexiones. Un usuario sugirió añadir soportes o tensores extra al mástil durante DTH muy profundo para mayor rigidez.
- Soporte técnico y repuestos: Dado que es un equipo de fabricación china, algunos compradores inicialmente se mostraron preocupados por la disponibilidad de repuestos. Las experiencias recientes indican que los distribuidores (por ejemplo, en Sudamérica) mantienen stock de repuestos comunes: sellos hidráulicos, bombas, filtros, etc., y que partes críticas como engranajes o componentes del motor Yunnei son relativamente estándar en maquinaria china. No obstante, se aconseja adquirir junto con la máquina un kit de repuestos críticos. En cuanto al soporte técnico, varias empresas proveedoras ofrecen asistencia remota y manuales detallados, aunque en algunos casos la barrera del idioma requirió traducciones. En resumen, los usuarios recomiendan asegurarse de contar con un buen respaldo del distribuidor local para garantizar la continuidad operativa.
En conjunto, las opiniones reales refuerzan la imagen de la M42-O como una solución rentable y versátil para perforaciones de mediana profundidad. Es apreciada por su capacidad de adaptarse a múltiples tareas y por su bajo costo operativo. Los operadores enfatizan la importancia de la pericia técnica (tanto en operación como en mantenimiento) para sacarle el máximo provecho. Bajo condiciones apropiadas y con un equipo humano competente, la M42-O ha demostrado ser fiable y cumplir con las necesidades de perforación de agua y exploración en terrenos mixtos, logrando profundidades cercanas a 300 m en numerosos proyectos exitosos.
Mantenimiento Preventivo Recomendado por Componente
Para asegurar la longevidad y el funcionamiento seguro de la M42-O, se debe seguir un estricto plan de mantenimiento preventivo que abarque todos sus sistemas. A continuación se detallan las tareas recomendadas para cada componente principal:
- Motor diésel: Revisar diariamente el nivel de aceite del motor y el estado del filtro de aire (limpiarlo o reemplazarlo si está muy sucio, especialmente en ambientes polvorientos). Cambiar el aceite del motor y filtro de aceite aproximadamente cada 150-200 horas de operación, o según recomendación del fabricante, utilizando el grado apropiado de aceite diesel. Drenar rutinariamente el sedimento/agua del filtro decantador de combustible y reemplazar los filtros de combustible cada 250 horas para prevenir obstrucciones. Verificar el nivel y concentración del refrigerante, asegurando que el radiador esté limpio de suciedad para evitar sobrecalentamientos. Engrasar los puntos de enlace del acelerador y verificar el estado de las correas (si el motor las usa para ventilador o alternador). Un motor bien mantenido garantizará la potencia continua necesaria para las demás funciones.
- Transmisión y cabezal mecánico: Cambiar el aceite de la caja de cambios y reductores del cabezal según las horas de trabajo (por ejemplo, cada 300 horas o 2 meses, lo que ocurra primero) utilizando aceite de engranajes de la viscosidad recomendada. Inspeccionar y ajustar el embrague periódicamente: verificar que no patine bajo carga; si se nota deslizamiento, ajustar la tensión del pedal o bombín (según tipo) y comprobar el estado de los discos. Revisar los engranajes y cojinetes del cabezal mediante las tapas de inspección o durante paradas mayores – buscar signos de desgaste excesivo o virutas en el aceite (lo cual indicaría desgaste interno). Mantener lubricados los puntos pivote del mecanismo de cambio de marchas. Nunca cambiar de marcha con la rotación en pleno torque; siempre desacoplar adecuadamente el embrague para evitar daño (esto forma parte de las buenas prácticas operativas más que de mantenimiento, pero es crucial para la vida del cabezal). Un mantenimiento preventivo riguroso en la transmisión asegurará que el cabezal conserve su desempeño óptimo y evita paradas por averías mayores.
- Sistema de avance y mástil: Inspeccionar diariamente el cilindro hidráulico principal y sus sellos – buscar fugas de aceite en vástagos y conexiones. Limpiar y lubricar las guías o carriles por donde desliza el cabezal en el mástil; quitar tierra, arcilla o residuos que se acumulen, y aplicar grasa ligera o aceite lubricante para evitar corrosión y atascos. Verificar la tensión y estado de la cadena o cable de izaje (si el mecanismo de avance usa poleas y cables para el doble recorrido): reemplazar cables deshilachados o cadenas con eslabones deformados inmediatamente. Comprobar los pernos de montaje del mástil al chasis y de los cilindros de elevación – deben estar apretados y sin holguras. Cada cierto tiempo, revisar la alineación del mástil (verticalidad) y ajustar los tensores o soportes si existieran. Este cuidado garantiza que el avance sea suave y que la carga se distribuya correctamente, evitando desgaste disparejo o trabas durante la perforación.
- Orugas y chasis: Engrasar a diario o al menos semanalmente todos los puntos del tren de rodaje: rodillos inferiores, rodillos superiores (si existen), ruedas guía delanteras y rueda motriz trasera. Esto prolonga la vida de los bujes y ejes. Comprobar la tensión de las orugas: una oruga demasiado floja puede salirse, y demasiado tensa causa desgaste; ajustar mediante los tornillos tensores según el manual (dejando la flecha adecuada). Limpiar las orugas de lodo seco, rocas o escombros que puedan alojarse en los eslabones. Revisar las zapatas (en orugas de caucho, buscar cortes o desprendimientos; en orugas de acero, revisar si hay zapatas dobladas o tornillos flojos). Inspeccionar el aceite de los motorreductores de orugas (si son de mando hidráulico) y cambiarlo anualmente. También chequear las mangueras hidráulicas que alimentan los motores de traslación por si hay rozaduras o fugas. En el chasis en general, apretar pernos estructurales y revisar soldaduras en busca de grietas (especialmente después de largos traslados por terreno accidentado). Mantener los gatos de nivelación en buen estado: lubricar las rótulas de sus patas, revisar que no pierdan aceite los cilindros y que las zapatas de apoyo no estén excesivamente gastadas. Todos estos pasos asegurarán que la movilidad y estabilidad del equipo no se vean comprometidas por falta de mantenimiento.
- Sistema hidráulico (bombas, válvulas y mangueras): Mantener el aceite hidráulico limpio y al nivel correcto en el tanque. Verificar el nivel cada día antes de operar y reponer si baja (baja indicaría posiblemente una fuga). Realizar cambios de aceite hidráulico y filtro a intervalos regulares – típicamente cada 500 horas – o antes si el aceite se contamina (pérdida de sus propiedades, cambio de color u olor a quemado). Limpiar o cambiar los filtros de succión y retorno según el manual (estos filtros son críticos para proteger las bombas y válvulas de partículas). Inspeccionar todas las mangueras hidráulicas en busca de abultamientos (signo de posible rotura interna), goteos en conexiones, o rozamiento contra superficies. Cualquier manguera dañada debe ser reemplazada inmediatamente, ya que una rotura durante operación puede ser peligrosa y causar pérdida de aceite. Revisar las bombas hidráulicas por ruidos anormales o variaciones de presión; medir la presión de alivio del sistema periódicamente para asegurarse de que las válvulas de alivio funcionan y están calibradas a la presión correcta. Engrasar los puntos articulados de las palancas de control. En climas fríos, calentar el sistema gradualmente al inicio de la jornada para evitar shock térmico en las bombas. Un sistema hidráulico bien mantenido evita paradas imprevistas y sostiene la fuerza de avance y funciones auxiliares con confiabilidad.
- Winche y cable de izaje: Inspeccionar antes de cada izaje importante el estado del cable de acero del winche principal. Pasar un trapo por el cable para detectar hilos cortados que puedan enganchar – si se encuentran más de 6 hilos rotos en un paso, es señal de reemplazo del cable. Asegurarse de que el cable esté correctamente enrollado en el tambor (sin cruzarse ni montarse) para evitar aplastamientos. Engrasar ligeramente el cable periódicamente con grasa especializada para cables, para reducir la corrosión y el desgaste por fricción. Probar el freno del winche: levantar una carga pequeña y verificar que al soltar el control el freno aguanta firmemente, sin deslizamiento. Ajustar el freno de banda o multidisco según corresponda, siguiendo las instrucciones del fabricante. Revisar los pernos de montaje del winche al mástil y el nivel de aceite de la caja del winche (si tiene reductora). En caso de winche hidráulico auxiliar, revisar su motor hidráulico y válvula de control de la misma manera que el resto del sistema hidráulico. Manteniendo el winche en buen estado se garantiza la seguridad en las maniobras de elevación de tuberías y equipamiento, evitando accidentes por fallo del cable o freno.
- Bomba de lodo y sistema de fluidos: Después de cada jornada de perforación con lodo, lavar la bomba de lodo con agua limpia para remover sedimentos de arcilla o cemento que pudieran asentarse en válvulas y tuberías. Nunca dejar lodo asentado en la bomba o las mangueras por largos periodos, pues puede endurecerse y obstruir el sistema. Revisar los empaques (sellos) de los pistones de la bomba de lodo; si se observan fugas de lodo por la tapa, es indicativo de empaquetadura desgastada que debe cambiarse. También monitorear las válvulas de succión y descarga de la bomba: limpiarlas y voltearlas si presentan desgaste desigual, o reemplazarlas si están erosionadas. Chequear el cárter de la bomba (si es lubricada por aceite) y cambiar ese aceite según especificaciones. En cuanto a las tuberías de lodo, inspeccionar las mangueras de alta presión, las uniones y abrazaderas – reapretar estas últimas y sustituir sellos si hay filtraciones. Mantener limpia la charola de lodo y los tanques, evitando que entre arena excesiva al sistema. Un mantenimiento diligente de la bomba de lodo asegura un flujo constante y evita interrupciones en la perforación por fallas en la circulación.
- Compresor y equipo neumático (auxiliar): Aunque el compresor de aire es un equipo externo, forma parte integral de las operaciones con la M42-O. Por ello, conviene incluirlo en la rutina de mantenimiento del proyecto. Revisar diariamente el filtro de aire del compresor y drenear los condensados del separador de humedad del compresor. Verificar los niveles de aceite del compresor (en el elemento tornillo o pistones) y del motor que lo impulsa. Controlar la temperatura de operación y limpiar los radiadores de aire/aceite del compresor para prevenir sobrecalentamientos. Inspeccionar las mangueras de aire altas presiones por desgaste o daños antes de conectarlas a la perforadora. Usar siempre líneas y coples certificados para la presión de trabajo (evitar mangueras improvisadas). Lubricar el martillo de fondo regularmente: muchas operaciones añaden aceite especial al aire (lubricador en línea) o vierten un poco de aceite en el martillo al inicio del día, para reducir su desgaste interno. Estas tareas garantizarán que la perforación neumática se realice sin contratiempos por falla del compresor o del martillo.
- Tuberías de perforación y herramientas: Cada vez que se manipulen las tuberías (por ejemplo, al agregar o quitar barras), limpiar y lubricar las roscas con grasa para rosca de perforación de buena calidad. Esto previene trabas y protege las roscas del desgaste y la corrosión. Inspeccionar visualmente las roscas en busca de daño (dientes deformados, fisuras); cualquier tubería con rosca comprometida debe repararse (re-cut) o retirarse de servicio para evitar que se atasque en la columna. Controlar la rectitud de las barras rodándolas en el suelo – una barra doblada causará vibraciones y desviación del pozo, por lo que debe enderezarse o desecharse. Mantener las barrenas tricónicas limpias y engrasadas cuando no se usen, y cubrirlas para proteger los cortadores. Revisar los sellos de rodamiento de las tricónicas y desechar la broca si los conos quedan flojos. En cuanto a los martillos DTH, hacerles mantenimiento periódico: desarmarlos según las horas de uso para cambiar los sellos internos y revisar el pistón y la camisa, eliminando residuos de polvo/roca. Guardar los martillos llenos de aceite para evitar oxidación interna. Las brocas de martillo (bits de boton) deben inspeccionarse para reafilado o reposición de botones de carburo si es posible, o ser reemplazadas cuando más del 30% de los botones estén gastados. Con los accesorios de diamantina, como barriles sacatestigo, limpiar bien el interior de la tubería, chequear la libre rotación del ensamblaje interno y lubricar los cojinetes si aplica; también inspeccionar las matrices de diamante de las coronas – reemplazarlas cuando se gasten hasta cierto punto para mantener buena velocidad de penetración. Por último, almacenar bajo techo o protegidos los accesorios sensibles (ej. un sampler SPT, tubos Shelby, etc.) y pintarlos o aceitaros para prevenir corrosión entre usos. En suma, cada herramienta debe recibir el cuidado adecuado tras su uso para estar en óptimas condiciones la próxima vez.
- Estructura general y seguridad: Verificar con frecuencia (mensualmente, por ejemplo) la estructura de la máquina: el apriete de todos los pernos críticos (mástil, chasis, soporte de cilindros), la integridad de las soldaduras y la ausencia de fisuras. Especial atención a la base del mástil, las orejas de anclaje de los gatos y las uniones de la torreta de orugas. Una grieta detectada a tiempo puede soldarse y reforzarse antes de que cause una falla mayor. Comprobar los pivotes de giro si el equipo tiene torreta giratoria (algunos modelos permiten cierto giro del mástil sobre el chasis) – en la M42-O parece fija, así que no aplica. Mantener en sitio extintores de incendio operativos (uno cerca del motor, otro en el área de bombas/compresor) y verificar sus cargas regularmente como parte de la seguridad preventiva.
Siguiendo este plan integral de mantenimiento preventivo, los propietarios han logrado que la M42-O funcione de forma confiable y segura a lo largo de los años. Muchas de las tareas descritas son de bajo costo y sencillas, pero marcan la diferencia para prevenir averías costosas y tiempos muertos. La clave es la constancia: establecer rutinas diarias, semanales y mensuales de inspección y servicio, y llevar un registro de mantenimiento. De esta manera, la perforadora estará siempre lista para operar al máximo de su rendimiento y con mínimos riesgos.
Comparación con Otras Perforadoras Chinas Similares (Cabezal Hidráulico)
Para poner en contexto a la M42-O, es útil compararla con otros modelos de perforadoras chinas de capacidad similar pero equipadas con cabezal rotativo hidráulico (es decir, top drives accionados por motor hidráulico). Estas máquinas hidráulicas de ~300 m de profundidad nominal existen en el mercado con distintas marcas, por ejemplo modelos tipo FY-300, HFDX-300, CWD300 entre otras. A continuación se presenta una comparación general de M42-O vs. una perforadora hidráulica típica de 300 m, abarcando aspectos de precio, desempeño y mantenimiento:
Aspecto | M42-O (Cabezal Mecánico) | Equipo Hidráulico 300m (Genérico) |
Precio estimado | ~USD 20–30 mil (equipo base). Muy accesible, menor costo inicial. | ~USD 40–60 mil (equipo chino hidráulico similar). Inversión inicial más alta. |
Potencia de motor | 42 kW (motor diésel Yunnei). Menor requerimiento de potencia gracias a alta eficiencia mecánica. | 75–90 kW (motores mayores). Necesita más potencia para alimentar bombas hidráulicas (pérdidas). |
Torque máximo | 9800 N·m. Alto torque disponible en marchas bajas (multiplicado mecánicamente). | ~5000–6500 N·m típico. Torque limitado por tamaño del motor hidráulico; adecuado para DTH mediano. |
Velocidad de rotación | 33–1120 rpm. Rango amplio (10 velocidades discretas); apto para coring de alta velocidad. | 0–150 rpm aprox. (variable continua). Control suave, pero sin capacidad de muy alta rpm (no ideal para diamantina rápida). |
Fuerza de tiro (pull-up) | 100 kN (10 Ton). Buena capacidad de izaje para su tamaño (puede sacar tubería entubada moderada). | ≥100 kN, a veces más (algunos modelos ~150–200 kN). Por lo general igualan o superan a la JDL en pull-up, gracias a cilindros hidráulicos grandes. |
Peso del equipo | ~3.8 ton (versión base). Más liviana, fácil de transportar pero menos masa estabilizadora. | 5–7 ton promedio. Más pesada, tiende a ser más estable en perforación profunda, pero complica el transporte. |
Facilidad de operación | Requiere operador experimentado para cambio de marchas, control manual de embrague y acelerador. Panel sencillo. | Operación más intuitiva con palancas/joysticks hidráulicos, control de rpm continuo. Menos intervención manual durante la perforación. |
Mantenimiento | Mecánica básica: Engranajes, embrague y motor diesel. Repuestos genéricos (sellos, filtros) fáciles de conseguir. Menos componentes de alta presión. | Hidráulica especializada: Necesita mantener bombas, motores y mangueras. Más componentes susceptibles a fugas. Requiere mayor control de limpieza de aceite. |
Fiabilidad | Alta, siempre que se realice mantenimiento preventivo. Menos sensores/eléctronica minimiza fallas inesperadas. Partes mecánicas robustas. | Alta también, aunque depende de la calidad de las bombas y componentes hidráulicos. Un descuido (aceite sucio) puede causar averías. Suelen incorporar sistemas automáticos de protección. |
Versatilidad de métodos | Muy versátil: lodo, aire, diamantina, SPT en uno solo. El gran rango de rpm le permite abarcar más métodos (incluyendo sondeo geológico rápido). | Versátil principalmente en pozos de agua y geotecnia convencional. Puede usar lodo y aire, pero pocos modelos hidráulicos alcanzan rpm tan altas para diamantina pura. |
Suavidad y precisión | Control menos refinado (velocidad en pasos). Posibles tirones al cambiar marcha. Mayor ruido/vibración. | Movimientos más suaves y precisos al regular hidráulicamente. Menor ruido y vibración percibida. |
Costos operativos | Menor consumo de combustible en general (menos HP). Mantenimiento económico (aceites, filtros baratos). Repuestos mecánicos suelen ser más económicos. | Mayor consumo de combustible (motor grande + pérdidas hidráulicas). Aceite hidráulico costoso y debe reemplazarse periódicamente. Componentes (bombas/motores) caros si fallan. |
Análisis comparativo: Como se observa, la M42-O sobresale en costo-beneficio y flexibilidad, haciéndola ideal para empresas pequeñas o medianas que requieran cubrir diversos tipos de trabajos sin adquirir múltiples equipos. Su cabezal mecánico le da una ventaja particular en trabajos de exploración con diamante o en combinaciones complejas de métodos en un mismo pozo. Además, en regiones donde el servicio técnico especializado es escaso, su mecánica simple puede ser atendida localmente.
Por su parte, las perforadoras hidráulicas de rango similar ofrecen una operación más sencilla (lo que puede traducirse en productividad ligeramente mayor si el operador es inexperto) y suelen tener sistemas automáticos de seguridad que previenen sobreesfuerzos. Por ejemplo, un equipo hidráulico puede limitar automáticamente la presión de avance para no romper una broca, o ajustar la velocidad según la carga, mientras que en la JDL eso recae más en el juicio del operador. Asimismo, en aplicaciones específicas como pozos de agua de gran diámetro (>300 mm) y profundidad moderada, un equipo hidráulico pesado con más pull-up podría instalar revestimientos más grandes con mayor facilidad.
En cuanto a fiabilidad, ambos tipos pueden ser confiables; sin embargo, un fallo hidráulico (por ejemplo, una bomba dañada) puede ser más difícil de solucionar en campo que un fallo mecánico (ej. un embrague) para el cual un buen mecánico local podría improvisar una reparación. Las máquinas hidráulicas modernas tienden a requerir un suministro eléctrico estable para sus controles, mientras que la M42-O puede funcionar completamente de forma autónoma sin depender de electrónica compleja.
En resumen, la elección entre la M42-O y un modelo hidráulico similar dependerá de las prioridades del usuario: economía y multipropósito vs. comodidad operativa y especialización. Para trabajos de exploración diversos y presupuestos ajustados, la M42-O ofrece una propuesta difícil de superar en su segmento. En cambio, para un programa intensivo de perforación de pozos de cierto diámetro con operarios menos especializados, una hidráulica podría justificarse por su simplicidad de uso y quizás mayor rendimiento en esa tarea específica. La Tabla 2 anterior sintetiza estos puntos comparativos clave para ayudar en la decisión.
Aplicaciones Típicas de la M42-O
La perforadora M42-O, por su carácter multifuncional, tiene múltiples aplicaciones en los campos de la geología, minería, ingeniería civil y provisión de agua. A continuación se enumeran las aplicaciones más comunes donde este modelo suele emplearse con éxito:
- Perforación de pozos de agua rurales: Esta es quizás la aplicación principal. La M42-O es ideal para pozos de agua profundos en comunidades rurales o pequeñas ciudades, donde se requieren profundidades de hasta 200–300 m para encontrar acuíferos confiables. Puede perforar pozos entubados de 4 a 10 pulgadas de diámetro para abastecimiento de agua potable, riego agrícola o uso ganadero. Su capacidad de lidiar con distintos estratos (arcillas, arenas, capas rocosas) la hace muy apta para zonas de geología variable. Además, su tamaño compacto permite movilizarla a sitios remotos, brindando solución de agua en lugares donde empresas más grandes no llegan. Proyectos de perforación de pozos comunitarios, riego rural y pozos domésticos se benefician de la M42-O por su eficiencia y bajo costo operativo en comparación con equipos mayores.
- Exploración geológica y minera (coring): La máquina se utiliza en campañas de exploración minera de depósito somero o mediano, donde se necesitan núcleos de roca para evaluar vetas minerales, contenidos metálicos, etc. También en exploración geotécnica profunda (por ejemplo, estudios de suelo y roca para presas, puentes o edificios altos) donde es necesario obtener testigos y datos de las capas subyacentes. En estas aplicaciones, la M42-O funciona como un equipo de sondaje: perfora con método diamantino y recupera núcleos (NQ, HQ típicamente) de las formaciones objetivo. Si bien no alcanza las profundidades de una sonda de núcleo grande (que pueden ser >1000 m), es más que suficiente para exploraciones de mediana profundidad (300–500 m) e investigaciones geológicas generales. Su ventaja es que el mismo equipo, tras tomar núcleos, puede ampliarse a un diámetro mayor (con tricona) y convertirse en un pozo de agua o en un pozo de monitoreo, todo en una misma plataforma, ahorrando movilizaciones.
- Hidrología y pozos de monitoreo: En el campo de la hidrogeología, la M42-O se usa para perforar pozos de observación de nivel freático, pozos de recarga, e instalar piezómetros. Dado que puede perforar con poco diámetro a gran profundidad, es ideal para pozo de monitoreo profundos. Además, en estudios de aguas subterráneas, a menudo hay suelos blandos arriba y roca abajo – escenario donde la dualidad lodo/aire es muy útil. También en proyectos de geotermia somera (por ejemplo, instalación de intercambiadores de calor de circuito cerrado en pozos de 100–150 m) este equipo se ha empleado, perforando múltiples pozos estrechos necesarios para sistemas de climatización geotérmica.
- Perforación geotécnica (fundaciones y estudios de suelo): Empresas de geotecnia utilizan la M42-O para sondeos de reconocimiento de suelos donde se requiere realizar SPT, toma de muestras inalteradas y en ocasiones instalar inclinómetros o piezómetros en el mismo agujero. La capacidad de la máquina para realizar SPT y extraer núcleos la hace una solución económica para investigaciones geotécnicas completas con un solo equipo. Además, para ciertas fundaciones profundas (pilotes) de pequeño diámetro o micropilotes, la M42-O puede perforar los barrenos guía. Por ejemplo, en la estabilización de taludes con anclajes, su tamaño compacto en orugas le permite posicionarse en laderas para perforar barrenos inclinados (en el modelo XJDL inclinable) e instalar barras de anclaje o cables. En pilotes de diámetro moderado (200–250 mm) y 20–30 m de profundidad para cimentaciones, podría usarse con las herramientas adecuadas, aunque para pilotes masivos se prefieren equipos de mayor tonelaje.
- Pozos de irrigación agrícola: Similar a pozos de agua potable, pero enfocado a riego agrícola en fincas y haciendas. Suele requerir perforar varios pozos de ~150 m en distintos puntos de un terreno. La M42-O permite moverse dentro de la finca con facilidad y perforar cada pozo eficientemente, incluso atravesando cantos rodados o capas duras con el martillo neumático cuando sea necesario. Muchos clientes la adquieren justamente para desarrollar campos de cultivo independientes del riego superficial. La maquina puede perforar e inmediatamente reamed el pozo a mayor diámetro si se desea más caudal, demostrando flexibilidad también en el tamaño del pozo.
- Zonas montañosas y de difícil acceso: Gracias a su diseño, la M42-O es especialmente útil en proyectos en zonas montañosas o aisladas, como se indica en la documentación del fabricante. Por ejemplo, abastecimiento de agua en comunidades andinas de altura, o perforación de pozos en islas, donde transportar un equipo grande sería complejo. Las orugas de caucho le permiten ascender por caminos estrechos y pendientes pronunciadas hasta llegar al punto de perforación. Se cita su uso en proyectos de captación de agua en áreas montañosas y formaciones rocosas donde usualmente se requiere perforar en roca dura para encontrar venas de agua. En esos entornos, la opción de usar DTH con compresor portátil es clave. Asimismo, en operaciones mineras de exploración en cordillera, su transporte relativamente sencillo (incluso desmontable en partes si fuese necesario con helicóptero) la hace preferible a sistemas más voluminosos.
- Aplicaciones especiales: La M42-O también puede adaptarse a aplicaciones fuera de lo común. Por ejemplo, en perforación de pozos de alivio o drenaje alrededor de presas o laderas inestables (para alivianar la presión de agua subterránea). En búsqueda de acuíferos profundos o estudios científicos del subsuelo donde se necesiten muestras de roca a profundidades intermedias. Incluso se ha mencionado su potencial uso en pozos de monitoreo ambiental (instalación de tuberías para muestreo de agua subterránea contaminada) e inyección de aguas pluviales (well injection) gracias a que puede perforar múltiples agujeros relativamente rápido con mínimo impacto.
En definitiva, las aplicaciones típicas de la M42-O abarcan desde la obtención de agua (su principal rol) hasta la exploración del subsuelo para minería o ingeniería civil. Su carácter polivalente es especialmente valorado en proyectos integrales, por ejemplo: un estudio hidrogeológico que requiera sondeos exploratorios con testigo, luego la construcción de un pozo de bombeo, y finalmente la instrumentación del acuífero con piezómetros – todo ello puede lograrse con esta única máquina. Esto la convierte en una herramienta sumamente atractiva para compañías consultoras e instituciones gubernamentales que atienden zonas rurales, donde un día puede estar perforando un pozo de agua y al siguiente un sondeo de reconocimiento en un camino próximo. El hecho de que combine funciones que tradicionalmente requerirían dos o tres equipos distintos es su mayor ventaja en el campo de las aplicaciones.
Recomendaciones para Operación, Seguridad y Transporte
Para finalizar este informe, es importante destacar una serie de recomendaciones prácticas al operar la M42-O, con énfasis en la seguridad de las operaciones y en las mejores prácticas para su transporte y movilización. Seguir estas pautas ayudará a prevenir accidentes, garantizar un desempeño eficiente y prolongar la vida útil del equipo.
Operación Segura y Eficiente
- Capacitación del operador: Asegurarse de que el operador (y asistentes) hayan recibido entrenamiento específico en el manejo de la M42-O. Deben conocer el funcionamiento de la caja de cambios, el embrague, los controles hidráulicos y las respuestas del equipo en diferentes modos de perforación. Practicar en condiciones controladas antes de acometer perforaciones profundas. Una operación competente no solo es más productiva, sino que reduce riesgos de daño al equipo (por ejemplo, no forzar marchas, detectar a tiempo sonidos anómalos).
- Inspección pre-operativa: Antes de cada jornada, realizar una lista de chequeo de seguridad: verificar que todos los pernos críticos estén ajustados, que no haya fugas de aceite o combustible, que los niveles de fluidos (motor, hidráulico, compresor) sean correctos, el estado del cable de winche, la presión de las líneas hidráulicas, y que los dispositivos de seguridad (freno del winche, freno de estacionamiento de orugas, etc.) funcionen. Comprobar también que los extintores estén en su lugar y cargados, y que las áreas de trabajo estén despejadas.
- Estabilización y nivelación: Siempre nivelar bien la máquina usando los gatos hidráulicos antes de iniciar la perforación. Un equipo desnivelado puede provocar desviación del pozo y es más propenso a volcar en terrenos inclinados. Colocar tablones robustos o placas bajo los gatos si el suelo es blando para distribuir la carga. No comenzar a perforar hasta que el mástil esté perfectamente vertical (verificado con nivel de burbuja o plumada). Durante la operación, monitorear periódicamente la nivelación, ya que el asentamiento del terreno o vibraciones pueden aflojar algún apoyo.
- Operación de la transmisión: Utilizar el embrague y cambio de marchas correctamente. Nunca intente engranar una marcha distinta mientras el cabezal está bajo carga o girando a altas rpm; primero desacelere el motor, pare la rotación si es necesario, luego realice el cambio suave de marcha y vuelva a acelerar progresivamente. Esto evitará daños en los engranajes. Emplear la marcha adecuada para cada etapa: marchas bajas para iniciar el agujero o en roca dura, y marchas altas para perforar rápido en formaciones blandas con barrena o diamante. Si se percibe que el motor se esfuerza demasiado o baja mucho de revoluciones, es señal de cambiar a una marcha inferior. Un oído atento al sonido del motor ayuda a tomar estas decisiones.
- Control de peso sobre la broca: Aprovechar el control hidráulico de avance para regular la presión sobre la herramienta de corte. En suelo blando, no aplicar peso excesivo para evitar enterramiento de la barrena; en roca dura con tricona, aumentar gradualmente hasta alcanzar la presión óptima de mordida sin sobrecargar. Recordar que en DTH, el peso sobre el martillo debe ser el suficiente para mantenerlo en el fondo, pero el trabajo lo hace la percusión (no presionar demasiado ya que se desperdicia energía y se frena la percusión). Estar atento a las indicaciones del manómetro de presión de avance si lo hay, y a las reacciones de la máquina (vibraciones, tasa de penetración) para ajustar en consecuencia.
- Monitoreo constante: Durante la perforación, monitorear continuamente todos los parámetros: presión y caudal de lodo (si perfora con lodo, vigilar que salga retorno con recortes; si deja de salir, posiblemente hay un atasco), presión del compresor y retorno de detritos (en aire, chequear que salga el detrito y que la presión no suba de golpe, indicativo de obstrucción), temperatura del motor y aceite hidráulico en sus respectivos indicadores, nivel de combustible, etc. Nunca dejar el equipo funcionando sin supervisión directa. Ante cualquier sonido inusual (golpeteo, chirrido) o vibración anómala, detenerse para investigar la causa – podría ser una broca desgastada, un cojinete en problemas, o una tubería suelta.
- Comunicación y coordinación: Mantener un sistema de comunicación claro con el ayudante o ayudantes en sitio. Utilizar señas o radios para coordinar acciones como subida/bajada de tuberías con el winche, adición de barras, arranque/parada del bombeo de lodo, etc. Solo una persona (generalmente el perforista principal) debe dar las indicaciones para evitar confusiones. Antes de operaciones críticas (como extraer un tramo de tubería), hacer un breve repaso verbal de los pasos con el equipo humano para que todos estén sincronizados.
Seguridad del Personal
- Uso de EPP: Todo el personal alrededor de la perforadora debe llevar Equipo de Protección Personal adecuado: casco, guantes de cuero (para manipular tuberías y cable), lentes de seguridad (especialmente si hay fragmentos de roca volando con aire), calzado de seguridad con puntera reforzada, y protección auditiva (orejeras o tapones) porque el ruido del motor, compresor y martillo puede superar los niveles seguros en proximidad prolongada. En trabajos con lodo, impermeables o trajes de agua pueden ser necesarios. Es responsabilidad del supervisor asegurar que nadie esté sin EPP en la zona de trabajo.
- Zona de exclusión: Delimitar una zona de trabajo segura alrededor de la máquina, donde solo el personal autorizado pueda ingresar. Especialmente cuando se esté manejando el winche o sacando tuberías, nadie debe situarse debajo de cargas suspendidas o en línea con el cable tenso. Colocar barricadas o cintas de peligro alrededor, manteniendo alejados a observadores o curiosos a una distancia prudente (mínimo 10 m). Si es un área pública, considerar vallado perimetral. También, cuando la perforadora está en uso, prohibir la presencia de personas en la línea del varillaje rotatorio (es decir, al frente o detrás del mástil) porque en caso de rotura de tubería o proyección de fragmentos, esas serían zonas de impacto.
- Atención a partes en movimiento: Identificar todas las partes móviles expuestas – el varillaje rotatorio, las poleas, ventilador de motor, cadenas, etc. – y evitar el contacto con ellas. Nunca tocar el varillaje mientras esté rotando; incluso detener la rotación completamente antes de acercar las manos para roscar o desroscar manualmente. Si se debe orientar la tubería con la mano, que sea únicamente cuando esté completamente detenida la rotación y el freno aplicado. Evitar ropa holgada, joyas, cabello suelto que pueda engancharse en el varillaje o engranajes. Instalar, si es posible, protecciones o guardas en puntos peligrosos (por ejemplo, alrededor de las poleas del winche) para minimizar la posibilidad de atrapamiento. En caso de que algo se atasque en la rotación (por ejemplo, un cable suelto), detener inmediatamente el equipo y desenergizar antes de intentar liberarlo.
- Procedimiento ante obstrucciones/atascos: Si la broca o martillo se atasca en el fondo (no avanza y el torque sube abruptamente o el compresor se “ahoga”), no insistir forzando, ya que podría romper la tubería o sobrecalentar el equipo. En su lugar, seguir un procedimiento de liberación: parar rotación, intentar invertir el giro lentamente para ver si sale; si no, levantar ligeramente con el avance para soltar la obstrucción; bombear lodo a presión o inyectar aire para limpiar. Es un momento donde se requiere calma y pericia. Tener un plan para recuperar herramientas atrapadas (fishing tools) y no arriesgar la integridad del taladro por apresuramiento.
- Manejo del lodo y recortes: El lodo de perforación puede generar un área muy resbaladiza alrededor de la perforadora. Es importante mantener orden y limpieza: encauzar el retorno de lodo a una fosa o tinas mediante canaletas, evitando charcos aleatorios. Retirar periódicamente los recortes y material expulsado para que no formen montículos en el área de circulación peatonal. El personal debe moverse con precaución sobre terreno fangoso o húmedo. Asimismo, controlar el polvo en perforación en seco con aire: puede ser necesario mojar la zona o usar coletores de polvo si se trabaja cerca de viviendas. La inhalación de polvo de sílice u otras partículas de roca es peligrosa; por ello, los operarios deberían usar mascarillas o respiradores al estar expuestos a polvo denso, y asegurarse de ventilar la zona.
- Paros de emergencia: Asegurarse de que todos sepan cómo detener la máquina rápidamente ante una emergencia. Identificar el botón de paro de emergencia (si está equipado) o cuál es la secuencia (por ejemplo, bajar el acelerador a ralentí y desembragar, o en casos extremos apagar el motor). En situaciones como atrapamiento de alguien, vuelco inminente, incendio, etc., detener todo movimiento es prioritario. Realizar simulacros mentales de qué haría cada miembro del equipo en ciertos escenarios de emergencia, de modo que si ocurre realmente, respondan con rapidez y coordinación.
Recomendaciones para Transporte y Movilización
- Preparación para transporte: Antes de trasladar la máquina de un sitio a otro, hay que configurarla para transporte seguro. Eso incluye bajar completamente el mástil a posición horizontal (o retraerlo/plegarlo si el diseño lo permite), fijar o trabar el cabezal y cualquier parte móvil para que no se mueva durante el viaje (muchos equipos tienen seguros mecánicos para el mástil y los gatos). Retirar las herramientas pesadas del mástil (por ejemplo, quitar el martillo DTH o la broca pesada y guardarlos aparte) para bajar el centro de gravedad. Drenar los tanques de lodo y vaciar tuberías si quedan llenas, para reducir peso y evitar derrames en el camino. Envolver o asegurar las mangueras sueltas y cables. Básicamente, dejar el equipo en su “posición de transporte” compacta – la M42-O en transporte mide ~4.6 m de largo, 1.9 m ancho, 2.5 m alto, dimensiones que caben en un camión estándar o contenedor de 20 pies.
- Carga en camión/remolque: Si la distancia a mover es significativa, es preferible cargar la perforadora en un camión cama baja, tráiler o remolque. Dado su peso (3.8 t), un camión de 5 toneladas o más es adecuado. Subirla autopropulsada con sus orugas si es posible: usar rampas robustas con capacidad de carga suficiente y ángulo moderado; alguien debe guiar al operador al subirla para alinear bien. Mantener baja velocidad y evitar maniobras bruscas al subir. Una vez sobre la plataforma, apagar el motor, colocar el freno de orugas (o calzar las orugas con bloques) y amarrar la máquina con cinchas o cadenas de amarre en al menos cuatro puntos (ojales del chasis diseñados para izaje/transporte). Apretar bien las estrobos de modo que la perforadora no pueda deslizarse ni tambalear. Si el mástil excede la altura legal, considerar desmontar partes o anglarlo; sin embargo, en este caso con 2.5 m de alto no suele haber problema.
- Transporte por carretera: Cumplir con las normativas de transporte pesado de la región: banderas rojas o luces si sobresale, permisos especiales si excede peso por eje (no usual en este tamaño), etc. Conducir el vehículo de transporte a velocidad moderada, evitando frenazos o giros bruscos que pudieran desplazar la carga. Recordar que una máquina de orugas amarrada puede aún moverse ligeramente en saltos, por lo que es mejor prevenir movimientos violentos. Revisar los amarres en las paradas durante el trayecto, apretar si alguno se aflojó.
- Descarga y desplazamiento en sitio: Al llegar a la nueva ubicación, escoger un terreno firme y relativamente nivelado para descargar. Usar nuevamente rampas adecuadas; si el sitio es complicado (p. ej. pendiente lateral), considerar usar un winche externo o un vehículo para asegurar la máquina con un cable mientras baja por la rampa, como respaldo en caso de resbalar. Una vez en tierra, moverla con sus orugas lentamente, planificando la ruta para evitar zanjas, pendientes excesivas o suelos donde pueda atascarse. En inclinaciones, siempre mantener el mástil hacia el lado alto (para evitar vuelco) y avanzar con mucha precaución; la especificación dice 25–30° de capacidad de ascenso, pero es prudente usar valores menores en la realidad y nunca con el mástil extendido. Si el suelo es muy blando (pantano, arena floja), evaluar crear un camino con tablones o usar planchas metálicas bajo las orugas para que no se hundan.
- Movilización autónoma a cortas distancias: Para distancias cortas entre pozos dentro de una misma obra, se puede desplazar la M42-O por sus propios medios. En ese caso, retirar la tubería y herramientas del pozo actual, asegurar todo, retraer mástil un poco (no moverla con el mástil completamente erguido y cargado con barras). Subir los gatos y avanzar con el personal guiando desde delante, vigilando obstáculos. Moverla únicamente en terreno suficientemente firme y plano; si hay que subir una ladera, valorar hacerlo en vacío (sin tuberías cargadas) y quizá con ayuda (jalando con un bulldozer o malacate si es muy empinada).
- Protección de la máquina en transporte: Si la máquina va a viajar largas distancias o a alta velocidad (por ejemplo en un camión por autopista), es recomendable proteger componentes sensibles: cubrir la consola de control con una lona para que el viento no dañe los manómetros o palancas; asegurar las tapas de depósitos de combustible e hidráulico; cubrir la entrada de aire del motor. También proteger el motor y partes hidráulicas de la lluvia si estará expuesta durante días en tránsito. En viajes internacionales (barco, etc.), embalar partes delicadas con plástico o lonas reforzadas contra la salinidad.
- Almacenamiento y estacionamiento seguro: Cuando la máquina no esté en uso (por ejemplo en temporada baja), guardarla preferiblemente bajo techo o al menos tapada con lona resistente. Dejarla apoyada en sus gatos para descargar peso de las orugas. Engrasar todas las partes antes de almacenarla para prevenir corrosión. Si va a estar meses detenida, drenar el combustible o agregar aditivo para que no se degrade, y cubrir los cilindros hidráulicos cromados con grasa o protecciones para que no se piquen. Desconectar la batería del motor para que no se descargue. Bloquear accesos para evitar uso no autorizado o vandalismo. Un almacenamiento adecuado preservará la máquina lista para la siguiente campaña de trabajo sin sorpresas.
Consideraciones Adicionales de Seguridad Operativa
- Condiciones climáticas: Evitar operar bajo tormentas eléctricas (por peligro de rayo en el mástil) o vientos fuertes que puedan comprometer la estabilidad del mástil. En caso de lluvia intensa, tener cuidado con el terreno fangoso bajo las orugas y los gatos – si empieza a ceder, detener la operación. Con bajas temperaturas, calentar el motor y sistema hidráulico gradualmente; con temperaturas muy altas, vigilar más de cerca la temperatura del motor y aceite (descansar la máquina al mediodía de ser necesario para enfriar). Siempre adaptar las operaciones al clima para mantener la seguridad.
- Seguridad en manejo de tuberías pesadas: Las varillas y tubos de revestimiento pueden ser pesados (decenas de kilos). Usar técnicas adecuadas de levantamiento (doblar rodillas, no la espalda, y ojalá entre dos personas) o emplear el winche auxiliar para posicionar tuberías en la boca del pozo. Nunca situar las manos cerca de las uniones al apretar con llaves – las llaves pueden resbalar y causar pellizcos graves, por lo que se recomienda guantes y mantener manos alejadas de la trayectoria de las llaves. Al romper la unión de una barra, estar preparado para su peso súbito (que no caiga descontroladamente).
- Atención a los gases en perforación: Si se perfora en terrenos con posibles bolsas de gas (por ejemplo, gas metano en turba, o grietas con gas natural en formaciones petrolíferas), tener detectores de gas presentes. Aunque es más propio de perforaciones profundas de hidrocarburos, incluso en pozos de agua ha habido incidentes con gas metano. Si se detecta gas, ventilar la zona, apagar cualquier llama (no fumar cerca del pozo), y evaluar las medidas a seguir (como instalar un venteo). En espacios cerrados (p.ej. perforando dentro de un túnel o sótano), la ventilación es crucial por acumulación de monóxido u otros gases de escape.
- Documentación y permisos: Asegurarse de contar con los permisos de perforación necesarios si la jurisdicción los requiere (muchas zonas exigen licencias para pozos de agua, notificación de uso de equipo pesado, etc.). Llevar registros de los sondeos (profundidad, estratos, horas de perforación) no solo por cumplimiento legal sino para referencia técnica. Asimismo, cumplir normativas ambientales: disposición correcta de los lodos extraídos, protección de acuíferos superficiales mediante entubación apropiada, etc.
- Uso de señales visuales y auditivas: Equipar la máquina con un alarma de retroceso audible al desplazarse en orugas para alertar a personas cercanas. Utilizar luces estroboscópicas si se trabaja de noche. Mantener iluminación adecuada en el área de trabajo nocturno – torres de luz o focos en el mástil – para que todos los movimientos sean visibles. La seguridad en operación nocturna requiere redundar en comunicaciones y señalización.
- Plan de respuesta a emergencias: Tener un plan claro por escrito o de conocimiento común ante emergencias: localización del botiquín de primeros auxilios, ruta al centro médico más cercano, contactos de emergencia. En caso de lesión, detener el trabajo y atenderla; para incidentes mayores (vuelco del equipo, atrapamiento), tener definido roles (quién llama a emergencias, quién intenta liberar con medios disponibles, etc.). La anticipación es vital para manejar bien un evento no deseado.
Siguiendo estas recomendaciones, la operación de la perforadora M42-O se puede realizar de forma segura, eficiente y con confianza. La clave está en combinar el conocimiento técnico del equipo con una cultura de seguridad proactiva, donde prevenir es mejor que lamentar.
En conclusión, la máquina perforadora M42-O con cabezal mecánico es una herramienta poderosa y versátil, cuyo aprovechamiento pleno depende tanto de sus bondades técnicas como de la pericia y cuidado con que sea utilizada y mantenida. Con los debidos resguardos y prácticas aquí descritas, la M42-O puede brindar años de servicio productivo en muy diversas aplicaciones, cumpliendo con las expectativas de quienes buscan una solución integral y económica para perforaciones en terrenos mixtos de hasta 300 metros de profundidad.
Venta de máquina perforadora
En El Gran Perforista somos importadores directos de maquinaria de perforación y trabajamos con equipos seleccionados por su calidad, rendimiento y confiabilidad en campo. No revendemos productos genéricos sin respaldo. Cada perforadora que ofrecemos está respaldada por especificaciones técnicas claras, asesoramiento antes y después de la compra, y repuestos disponibles.
📦 Condiciones de compra
- Se realiza una entrega inicial del 50% para iniciar el pedido.
- El saldo se paga al momento de entrega del equipo.
- Tiempo estimado de entrega: entre 60 y 90 días.
- Las entregas se realizan en nuestros depósitos en Río Tercero, Córdoba, o con envío a cargo del cliente.
Contactanos para recibir el presupuesto formal: